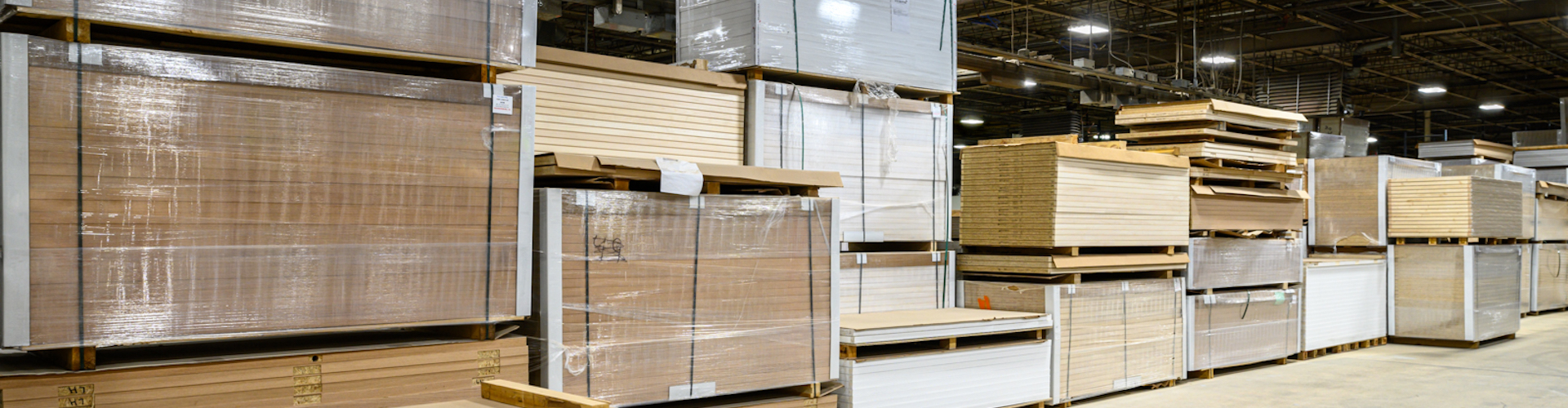
Door Glossary
A Moulding Or Trim Attached To The Meeting Edges Of Adjacent Door Leaves In Order To Prevent Swing Through And To Conceal The Gap. Also May Be Used For Sound Control, Bullet Resistance And X-Ray Shielding.
Two Or More Veneer Components Or Leaves Of Equal Size (Prior To Edge Trimming) To Make Up A Single Face.
A Narrow, Horizontal, Vertical, Or Diagonal Wood Member Extending The Total Length Or Width Of A Glazed Opening, Used To Separate Individual Pieces Of Glazing.
An Effect In Book Matching Of Veneers. Because The “Tight” And “Loose” Sides Alternate In Adjacent Veneer Leaves, They May Accept Stain Or Reflect Light Differently, Resulting In A Noticeable But Acceptable Color Variation. Barber Pole Is Not Considered A Manufacturing Defect.
Comparatively Small Area Of Bark Around Which Normal Wood Has Grown.
A Machine Angle Other Than A Right Angle, I.E., A 3 Degree Bevel That Is Equivalent To A 1/8 Inch Drop In A 2 Inch Span (1 Mm In 16 Mm).
An Edge Of The Door Which Forms An Angle Of Less Than 90 Degrees With The Face Of The Door, Such As A 3 Degree Beveled Edge.
A Mark Or Wound In A Tree Or Piece Of Wood Caused By Birds Pecking On The Growing Tree In Search Of Insects.
See “Membrane Pressed Panel”.
A Repair Referring To End Splits, Repaired With Wood Or Filler Similar In Color To Blend Well With Adjacent Wood.
Color Change That Is Detectable At A Distance Of 6 Ft. To 8 Ft. (1.8 M To 2.4 M) But Which Does Not Detract From The Overall Appearance Of The Door.
A Method Of Construction Of Stile And Rail Wood Doors Where Openings Are Machined Into, But Not Through The Stiles And Where The Ends Of The Rails Are So Machined As To Fit These Openings.
Spot Or Area Where Veneer Does Not Adhere.
A Material Used To Replace Core Material In Specific Locations To Provide Improved Screw Holding For The Attachment Of Hardware. Blocking Is Only Required Where The Screw Holding Power Of The Core Is Less Than Required By The Applicable Performance Duty Level.
Stiles And Rails (Edge Bands) Are Securely Glued To The Core Prior To Application Of Crossbanding, Three Ply Skins, Veneers Or Laminate.
Adjacent Leaves Of Veneer From A Flitch Or Log Are Opened Like A Book And Spliced To Make Up The Face With Matching Occurring At The Spliced Joints. The Fibers Of The Wood, Slanting In Opposite Directions In The Adjacent Leaves, Create A Characteristic Light And Dark Effect When The Surface Is Seen From An Angle.
The Height And Width Of A Door Prior To Prefitting.
A Flat Wise Deviation From A Straight Line Drawn From Top To Bottom; A Curvature Along The Length Of The Door.
A Condition Of Wood Characterized By A Low Resistance To Shock And By Abrupt Failure Across The Grain Without Splintering.
Doors That Resist Penetration By Shots Of Varying Caliber. Resistance May Be Rated As Resistant To Medium Power, High Power, Or High Power Small Arms And High Power Rifles.
A Swirl, Twist Or Distortion In The Grain Of The Wood, Which Usually Occurs Near A Knot Or Crotch. A Burl Can Often Be Associated With Abrupt Color Variation And/Or A Cluster Of Adventitious Buds.
A Swirl, Twist Or Distortion In The Grain Of The Wood Which Usually Occurs Near A Knot Or Crotch But Does Not Contain A Knot And Does Not Contain Abrupt Color Variation.
A Joint Formed By Square Edge Surfaces (Ends, Edges, And Faces) Coming Together; End Butt Joint, Edge Butt Joint.
A Grain Appearance Characterized By A Series Of Stacked And Inverted “V”S, Or Cathedral Type Of Springwood (Earlywood) Summerwood (Latewood) Patterns Common In Plain Sliced (Flat Cut) Veneer (See Split Heart).
An Even Number Of Veneer Components Or Leaves Of Equal Size (Prior To Edge Trimming) Matched With A Joint In The Center Of The Panel To Achieve Horizontal Symmetry.
Wood Products That Have Been Qualified By An Independent Third Party Agency As Satisfying Their Proprietary Requirements For Responsible Environmental Practices.
Line Appearing Across The Face At Right Angles To The Grain Giving The Appearance Of One Or More Corrugations Resulting From Bad Setting Of Sanding Equipment.
Small Slits Running Parallel To Grain Wood, Caused Chiefly By Strains Produced In Seasoning And Drying.
When A Defect Described In The Grading Rule Is Sufficient In Number And Sufficiently Close Together To Appear To Be Concentrated In One Area.
A Quality Of Rift Cut Veneer With Exceptionally Straight Grain And Closely Spaced Growth Increments Resembling The Appearance Of Long Stands Of Combed Hair.
When Relating Door Edge To Face Appearance, The Edge May Not Be The Same Species As The Face; However, It May Be Similar In Overall Color, Grain, Character And Contrast As The Face (See Matching Edge Band).
An Individual Piece Of Veneer Or Leaf That Is Joined To Other Pieces To Achieve A Full Length And Width Face.
A Composite Whose Ingredients Include Cellulosic Elements. These Cellulosic Elements Can Appear In The Form Of, But Are Not Limited To: Distinct Fibers, Fiber Bundles, Particles, Wafers, Flakes, Strands And Veneers. These Elements May Be Bonded Together With Naturally Occurring Or Synthetic Polymers. Also, Additives Such As Wax Or Preservatives May Be Added To Enhance Performance.
A Door Panel Composed Of A Wood Derivative Such As Mdf. Used For Opaque Finishes.
See ‘Burl, Conspicuous’ And ‘Knots, Conspicuous Pin’.
The End Of Rails, Mullions, Muntins Or Bars So Machined That They Will Fit And Cover The Contour Of The Sticking.
The Innermost Layer Or Section In Component Construction. For Typical Constructions See: Particleboard Core, Medium Density Fiberboard Core, Structural Composite Lumber Core, Staved Lumber Core, Laminated Veneer Lumber Core, Fire Resistant Composite Core And Other Special Core Types.
A Fire Resistant Core Material Generally Used In Wood Doors Requiring Fire Ratings Of 3/4 Hour Or More. Engineered Composite Products Meeting The Minimum Requirements Of Wdma.
Irregularity Of Grain Resembling A Dip In The Grain Running At Right Angles, Or Nearly So, To The Length Of The Veneer.
Separation (Break) Of The Wood Cells Across The Grain. Such Breaks May Be Due To Internal Strains Resulting From Unequal Longitudinal Shrinkage, Or To External Forces.
A Series Of Naturally Occurring Figure Effects Characterized By Mild Or Dominant Patterns Across The Grain In Some Faces. For Example, A Washboard Effect Occurs In Fiddle-Back Cross Figure; And Cross Wrinkles Occur In The Mottle Figure.
A Ply Placed Between The Core And Face Veneer In 5-Ply Construction Or A Ply Placed Between The Back And Face Of A 3-Ply Skin In 5-Ply Construction, Typically Of Hardwood Veneer Or Engineered Wood Product.
A Deviation From A Straight Line Drawn From Side To Side; A Curvature Along The Width Of The Door.
Openings Where A Portion Of The Wood Knot Has Dropped Out Or Where Cross Checks Have Occurred To Present An Opening.
The Decomposition Of Wood Substance By Fungi.
Checks, Splits, Open Joints, Knotholes, Cracks, Loose Knots, Wormholes, Gaps, Voids, Or Other Opening Interrupting The Smooth Continuity Of The Wood Surface.
Separation Of Plies Or Layers Of Wood Or Other Material Through Failure Of The Adhesive Bond.
Stains In Wood Substances. Some Common Veneer Stains Are Sap Stains, Blue Stains, Stain Produced By Chemical Action Caused By The Iron In The Cutting Knife Coming Into Contact With The Tannic Acid In The Wood, And Those Resulting From The Chemical Action Of The Glue.
A Group Of Components (Wood, Aluminum Or Steel) That Are Assembled To Form An Enclosure And Support For A Door. Also Known As Door Jambs.
Doors So Hinged As To Fold Against The Door Jamb. Bifold Doors Are Normally Classified As Either Two- Or Four-Leaf Units.
A Door Assembly Of Stiles And Rails That Will Include Multiple Door Types Within A Single Door. These Door Types Would Typically Include Combinations Of Flat Or Raised Panels, Lites And/Or Louvers.
A Door Assembly Of Stiles And Rails (And Possibly Muntins And Bars) Surrounding A Single Or Multiple Glazed Opening.
A Door Assembly Of Stiles And Rails Where The Interior Is Filled With Slat Or Chevron Louvers.
A Door Assembly Of Stiles, Rails And One Or More Panels. Intermediate Rails Or Mullions Are Used To Separate Panels. Panels Can Be Raised Or Flat.
A Method Of Construction Of Stile And Rail Wood Doors Where Holes Are Machined Into, But Not Through, The Stiles And Where Matching Holes Are Machined Into The Ends Of The Rails. Glue And Dowels Are Inserted Into These Holes To Attach The Rail To The Stile.
A Form Of Incipient Decay Characterized By Dull And Lifeless Appearance Of The Wood, Accompanied By A Lack Of Strength And Softening Of The Wood.
A Strip Along The Outside Edges Of The Two Sides And/Or Top And Bottom Of The Door (See Stiles/Vertical Edges, Rails/Horizontal Edges).
A Door/Transom Combination Where Single Piece Of Veneer Extends From The Bottom To The Top Of The Door With A Mirror Image At The Transom.
A Method Of Constructing A Wood Stile And Rail Door That Minimizes The Use Of Solid Lumber Components. Stiles, Rails And Mullions Have Solid Lumber Edges Only (Where Visible), And Have Face Veneers Over A Composite Core. Panels Are Also Produced Using Face Veneers And/Or Composite Cores.
A General Term Used To Describe Any Wood Or Plant Fiber Composite Panel. Such Products As Particleboard, Mdf, Scl And Lvl Are Described As Engineered Fiber. Typically They Are Made From Wood Or Plant Fiber Or Wood Pieces And Have Specific Quality Requirements.
Veneers That Are First Peeled, Normally From Obeche Or Poplar Logs. The Peeled Veneer Leaves Are Dyed To A Specified Color, And Then Glued Together In A Mold To Produce A Large Laminated Block. The Shape Of The Mold Determines The Final Grain Configuration. The Block Is Then Sliced Into Leaves Of Veneer With A Designed Appearance That Is Highly Repeatable.
The Outermost Exposed Wood Veneer Surface Of A Veneered Wood Door.
The Total Width Of The Stile, Rail Or Panel Minus The Width Of The Moulding Patterns. The Most Common Way Of Showing Dimensions On A Stile And Rail Door Elevation.
A Small Number Of Characteristics Without Regard To Their Arrangement In The Panel
A Repair To An Open Defect Usually Made With Fast Drying Plastic Putty. The Repairs Should Be Well Made With Non-Shrinking Putty Of A Color Matching The Surrounding Area Of The Wood, To Be Flat And Level With The Face And Panel, And To Be Sanded After Application And Drying.
A Series Of Interlocking Fingers Precision Cut On The Ends Of Two Pieces Of Wood Which Mesh Together And Are Held Rigidly In Place With Adhesive.
A Door Which Has Been Constructed In Such A Manner That When Installed In An Assembly Will Pass A Fire Test Under Neutral (Ul 10B) Or Positive (Ul 10C) Pressure Criteria And Can Be Rated As Resisting Fire For 20 Minutes (1/3 Hour), 45 Minutes (3/4 Hour), 1 Hour, Or 1-1/2 Hours. The Door Must Be Tested And Carry An Identifying Label From A Qualified Inspection Agency.
A Core, Typically Incorporating Minerals Rather Than Wood Fiber As The Primary Component, Designed To Improve Fire Resistance And Thermal Transmission
See Fleck, Ray.
See Plain-Sliced.
Portion Of A Ray As It Appears On The Quartered Or Rift Cut Surface. Fleck Can Be Dominant Appearance In Oak And Is Sometimes Referred To As Flake.
A Complete Bundle Of Veneer Sheets Laid Together In Sequence As They Are Cut From A Given Log Or Section Of Log.
Open Slits In The Inner Ply Or Plies Or Improperly Joined Veneer When Joined Veneers Are Used For Inner Plies.
A Small Wood Moulding (Bead) Applied To The Perimeter Of Glazed Openings To Secure The Glazing Materials Within A Door.
The Direction, Size, Arrangement And Appearance Of The Fibers In Wood Or Veneer.
Expression Of The Angle Of The Grain To The Long Edges Of The Veneer Component.
Expression Of The Angle Of The Grain To The Long Edges Of The Veneer Component Over A 12 Inch (300 Mm) Length From Each End Of The Door.
Well-Defined Opening Between Rings Of Annual Growth Containing Gum Or Evidence Of Prior Gum Accumulations. Mainly Cherry.
Gum Or Resinous Material Of Color Spots Caused By Prior Resin Accumulations Sometimes Found On Panel Surfaces.
A Thin, Perceptible Line Showing At The Joint Of Two Pieces Of Wood.
A Method Of Veneer Cutting Similar To Rotary Cutting, Except That The Piece Being Cut Is Secured To A “Stay Log” A Device That Permits The Cutting Of The Log On A Wider Sweep Than When Mounted With Its Center Secured In The Lathe To Produce Rotary Sliced Veneer. A Type Of Half-Round Cutting Is Used To Achieve Plain-Sliced Or Flat-Cut Veneer.
Homogeneous Panels Manufactured Primarily From Inter-Felted Lignocellulosic (Wood) Fibers Consolidated Under Heat And Pressure With Density Of 31 Lb/Ft3 (497 Kg/M3) Or More.
General Term Used To Designate Lumber Or Veneer Produced From Temperate Zone Deciduous Or Tropical Broad-Leaved Trees In Contrast To Softwood, Which Is Produced From Trees Which Are Usually Needle Bearing Or Coniferous. The Term Does Not Infer Hardness In Its Physical Sense.
The Non-Active Center Of A Tree Generally Distinguishable From The Outer Portion (Sapwood) By Its Darker Color.
No Longer Defined Under Ansi A208.2; Hdf Is A Marketing Term To Define Mdf Grades Above Grade 150
A High Impact Resistant Surface Material Consisting Of Decorative Surface Paper Impregnated With Melamine Resins Pressed Over Multiple Craft Paper Layers Saturated With Phenolic Resins, Thermoset At High Pressure And Temperature.
Holes Resulting From Infestation By Worms Greater Than 1/16 Inch (1.6 Mm) In Diameter And Not Exceeding 5/8 Inch (16 Mm) In Length.
Barely Detectable With The Naked Eye At A Distance Of 6 Ft. To 8 Ft. (1.8 M To 2.4 M).
Areas In The Face That Have Been Compressed As The Result Of Residue On The Platens Of The Hot Press Or Handling Damages.
A Material That Expands When Exposed To Extreme Heat Or Fire To Fill Any Gap Between The Door And Frame Or Between Doors.
The Line Of Juncture Between The Edges Or Ends Of Two Adjacent Pieces Of Veneer.
Joint Running Parallel To The Grain Of The Wood.
Joint In Which Two Adjacent Pieces Of Veneer Do Not Fit Tightly Together.
Lumber Dried In A Closed Chamber In Which The Removal Of Moisture Is Controlled By Artificial Heat And Usually By Controlled Relative Humidity.
A Measure Of The Smoothness Of Machined Lumber. Can Be Determined By Holding The Surfaced Board At An Angle To A Strong Light Source And Counting The Visible Ridges Per Inch, Usually Perpendicular To The Profile. The Surface Is Smoother With More Knife Marks Per Inch.
Very Fine Lines That Appear Across The Panel Veneer Or Wood Solids That Can Look As Though They Are Raised Resulting From Some Defect In The Lathe Knife That Cannot Be Removed With Sanding.
Cross Section Of Tree Branch Or Limb With Grain Usually Running At Right Angles To That Of The Piece Of Wood In Which It Occurs.
Voids Produced When Knots Drop From The Wood In Which They Were Originally Embedded.
Sound Knots 1/4 Inch (6.4 Mm) Or Less That Generally Do Not Contain Dark Centers. Blending Pin Knots Are Barely Detectable At A Distance Of 6 Ft. To 8 Ft. (1.8 M To 2.4 M), Do Not Detract From The Overall Appearance Of The Panel, And Are Not Prohibited From Appearing In All Grades.
Sound Knots 1/4 Inch (6.4 Mm) Or Less In Diameter Containing Dark Centers.
Openings Where A Portion Of The Wood Substance Of The Knot Was Dropped Out, Or Where Cross Checks Have Occurred To Produce An Opening.
Knots That Are Solid Across Their Face And Fixed By Growth To Retain Their Place.
Manufactured By Laminating Veneer With All Grain Laid-Up Parallel. It Can Be Manufactured By Using Various Species Of Wood Fiber In Various Thicknesses.
A Condition Where The Pieces Of Veneer Are So Misplaced That One Piece Overlaps The Other And Does Not Make A Smooth Joint.
A Concealed Block The Same Thickness As The Door Stile Or Core Which Is Adjacent To The Stile At A Location Corresponding To The Lock Location And Into Which A Lock Is Fitted.
In Knife-Cut Veneer, That Side Of The Sheet That Was In Contact With The Knife As The Veneer Was Being Cut, And Containing Cutting Checks (Lathe Checks) Because Of The Bending Of The Wood At The Knife Edge.
A Panel Constructed Of Wood Or Metal Slats Installed In An Opening To Allow Light, Air And Noise. Common Types Are Slat And Chevron – An Inverted “V” Wood Louver (Vented Or Non-Vented).
A Decorative Surface Paper That Is Saturated With Reactive Resins. During Hot Press Lamination, The Resin Flows Into The Surface Of The Substrate, Creating A Hard Crosslinked Thermosetting Permanent Bond And Permanently Changing The Characteristics Of Both The Paper And The Board.
An Edge Band That Is The Same Species Or Laminate Pattern As The Face Veneer.
The Generic Name For A Panel Or Core Manufactured From Lignocellulosic Fibers Combined With A Synthetic Resin Or Other Suitable Binder And Bonded Together Under Heat And Pressure In A Hot Press By A Process In Which The Added Binder Creates The Entire Bond.
Wood Fiber And/Or Agri-Fiber Based Materials That Comply With Ansi A208.2.
Typically Mdo Is Kraft Paper Saturated With Resin And Cured Under High Heat And Pressure To Make A Hard, Smooth, Paintable Surface.
Two Adjacent Door Edges Not Separated By A Mullion Or Transom Bar. These Are Found In Pair, Dutch Door And Door & Transom Applications.
Insert Panel Produced By Moulding To Profile A Wood Or Composite Core (Usually Mdf Or Particleboard) Then Pressing Veneer To The Core Using A Flexible Pressing Surface.
See Streaks, Mineral.
See Core, Fire Resistant.
Olive And Greenish-Black Streaks Believed To Designate Areas Of Abnormal Concentration Of Mineral Matter; Common In Hard Maple, Hickory, And Basswood. Also Called Mineral Streak.
Sharply Contrasting Elongated Discoloration Of The Wood Substance.
See “Blind Mortise And Tenon”
Profiled Wood Trim Pieces That Surround The Perimeter Of Panels Or Glazing, But Does Not Protrude Above The Surface Of The Surrounding Stiles And Rails.
A Vertical Member Used To Separate Panels. Also Known As A “Mull”.
A Short Bar, Either Horizontal Or Vertical, Used To Separate Individual Pieces Of Glazing Material, But Which Does Not Extend The Full Width Or Length Of The Glazed Opening. Also Known As “Munt”.
When Referring To Color And Matching, Veneers Containing Any Amount Of Sapwood And/Or Heartwood, I.E., Natural Birch, Maple, Ash.
A Fire Door Test Procedure Where The Neutral Pressure Plane Is Near The Top Of The Door.
A Term That Designates A Stated Dimension As Being Approximate And Subject To Allowances For Variation.
Stiles And Rails (Edge Bands) Are Not Glued To The Core Prior To Face Materials.
Allowed, Unlimited.
A Small Number Of Characteristics That Are Arranged Somewhat Diversely Within The Face.
A Door Panel In Which The Perimeter Does Not Contain A Machined Profile (Panel Raise). Constructed With Veneer On The Face And A Composite Core For A Stained Finish, Or Mdf For A Painted Finish.
A Door Panel Whose Faces Are Raised Above The Perimeter And Whose Edges Are Shaped To Fit Into Grooves In The Stiles, Rails And Mullions. These Panels Are Typically Bladder Pressed Or Rim Banded For A Stained Finish Or Mdf For A Painted Finish.
A Panel Or Core Product Composed Of Small Particles Of Wood And Wood Fiber That Are Bonded Together With Synthetic Resin Adhesives In The Presence Of Heat And Pressure.
Wood Fiber And/Or Agri-Fiber Based Materials That Comply With Ansi A208.1, Minimum Grade Ld-1.
Matching Wood Pieces Carefully Inserted And Glued Into The Door Face After Defective Portions Have Been Removed.
Veneer Sliced Parallel To The Pith Of The Log And Approximately Tangent To The Growth Rings To Achieve Flat Cut Veneer. Plain Sliced Veneer Can Be Cut Using Either A Horizontal Or Vertical Slicing Machine Or By The Half-Round Method Using A Rotary Lathe. Also Known As Flat Cut
A Face Containing Specially Selected And Assembled Dissimilar (In Color, Grain And Width) Veneer Strips Of The Same Species, And Sometimes Grooved At The Joints Between Strips, To Simulate Lumber Planking. Plank Matched Faces Are Not Available Pair Matched Or Set Matched.
A Face Containing Components, Which Provide A Pleasing Overall Appearance. The Grain Of The Various Components Need Not Be Matched At The Joints. Sharp Color Contrasts At The Joints Of The Components Are Not Permitted.
A Single Sheet Of Veneer Or Several Strips Laid With Adjoining Edges That May Or May Not Be Glued, Which Forms One Veneer Lamination In A Glued Panel. In Some Constructions, A Ply Is Used To Refer To Other Wood Components Such As Particleboard Or Mdf.
A Fire Door Test Procedure Where The Neutral Pressure Plane Is Located At 40 Inches (1 M) Above The Sill.
Trimming Of The Door For Width And/Or Height.
See Fill.
Veneer Produced By Cutting In A Radial Direction To The Pith To Achieve A Straight (Vertical) Grain Pattern. In Some Species, Principally Red Oak And White Oak, Ray Fleck Is Produced, The Amount Of Which May Be Unlimited.
A Horizontal Structural Member Of A Stile And Rail Door. Fits Between The Stiles.
The Bottom Rail Of A Stile And Rail Door
A Rail, Other Than The Top And Bottom Rail, Used To Separate Panels, Or To Separate Panels From Glazing Materials In A Combination Door. Also Referred To As “Cross Rail”.
An Intermediate Rail Located At Approximately Adjacent To The Lock.
The Uppermost Rail Of A Stile And Rail Door.
Top And Bottom Edge Bands Of Door.
A Face Containing Veneer Strips Of The Same Species Which Are Selected And Assembled Without Regard To Color Or Grain, Resulting In Variations, Contrasts And Patterns Of Color And Grain. Pleasing Appearance Is Not Required. Random Matched Faces Are Not Available Pair Matched Or Set Matched.
Ribbon-Shaped Strand Of Tissue Extending In A Radial Direction Across The Grain, So Oriented That The Face Of The Ribbon Is Exposed As A Fleck On The Quarter Surface. Also Known As Wood Ray.
See Fleck, Ray.
When Referring To Color And Matching, Veneers Containing All Heartwood, Ranging In Color From Light To Dark.
A Patch, Shim, Or Filler Material Inserted And/Or Glued Into Veneer Or A Panel To Achieve A Sound Surface.
Wood Or Filler Insertions Similar In Color To Adjacent Wood So As To Blend Well.
Veneer Produced By Cutting At A Slight Right Angle To The Radial To Produce A Parallel Grain Pattern And Quartered Appearance Without Excessive Ray Fleck. Oak Veneer Only.
Insert Panel With A Solid Lumber Edge Banded Around The Core Then Veneered And Profiled.
Veneer Produced By Centering The Entire Log In A Lathe And Turning It Against A Broad Cutting Knife.
Irregular Shaped Areas Of Generally Uneven Corrugation On The Surface Of Veneer.
The Veneer Face Is Made From Components Running Through The Flitch Consecutively. Any Portion Of The Component Left Over From A Face Is Used As The Beginning Component Or Leaf In Starting The Next Veneer Face.
A Break Or Breaks In The Grain Or Between Springwood And Summerwood Caused Or Aggravated By Excessive Pressure On The Wood By Seasoning, Manufacturing, Or Natural Processes. Ruptured Grain Appears As A Single Or Series Of Distinct Separations In The Wood Such As When Springwood Is Crushed Leaving The Summerwood To Separate In One Or More Growth Increments.
Lacking Excessive Refinement, Having A Rough Surface Or Finish.
Glazing Materials So Constructed, Treated Or Combined With Other Material As To Minimize The Likelihood Of Cutting Or Piercing Injuries Resulting From Human Contact With The Material. The Most Common Types Used In Doors Are Tempered Or Laminated. Safety Glazing Materials Are Required To Meet Codes And Federal Regulations.
The Degree Of Defects Allowed In Sanding Of The Face.
The Living Wood Of Lighter Color Occurring In The Outer Portion Of A Tree.
A Separation Along The Grain Of Wood In Which The Greater Part Occurs Between The Rings Of Annual Growth.
For The Purpose Of This Standard, This Term Means The Veneer Of Lighter Than Average Color Should Not Be Joined At The Edges With Veneer Of Darker Than Average Color, And That Two Adjacent Pieces Of Veneer Should Not Be Widely Dissimilar In Grain, Figure And Natural Character Markings.
A Split Repaired In A Piece Of Wood Veneer, Preferably From The Same Piece Of Veneer From Which The Face Is Made To Ensure Good Color And Grain Match. The Grain Running In The Same Direction As The Split To Be Inconspicuous To The Naked Eye, And Free Of Any Gaps Where The Shim Joins The Veneer. To Be Glued Into The Split And Sanded After Being Made. Color Matched.
A Defect Caused By The Outline And/Or Surface Irregularities, Such As Frame Parts, Core Laps, Voids, Etc., That Is Visible Through The Face Veneers.
The Face Layer Of A Flush Or Stile And Rail Door, Whether Flat Or Configured, Which Is Used For Facings For Flush Wood Doors.
Veneer Produced By Thrusting A Log Or Sawed Flitch Into A Slicing Machine, Which Shears Off Veneer In Sheets.
Visible On Observation, But Does Not Interfere With The Overall Aesthetic Appearance.
A Sheet From A Flitch Is Slid Across The Sheet Beneath And, Without Turning, Spliced At The Joint.
See Grain
Veneer Cut To Minimize Lathe Checks.
A Single Number Rating System Derived From Measured Values Of Sound Transmission Loss Or The Acoustical Performance Of A Building Element, Such As A Door, Window Or Wall. The Higher The Stc Value, The Better The Rating And The Better The Acoustical Performance Value. Tested In Accordance With Astm E413 And E90.
A Method Of Achieving An Inverted “V” Or Cathedral Type Of Springwood (Earlywood)/Summerwood (Latewood), Plain-Sliced (Flat-Cut) Figure By Joining Two Veneer Components Of Similar Color And Grain. A Cathedral Type Figure Must Be Achieved By A Single Component In Aa Grade; The Split Heart Method Is Allowed In Grades A And B. Each Half Of A Split Heart Shall Be Subject To The Minimum Component Width Requirements For Grade A And B Faces.
Separations Of Wood Fiber Running Parallel To The Grain.
A Perceptible Separation Or Absence Of Wood Fiber Running Parallel With The Grain.
By Industry Practice, A Standard Door Is Book Size In Both Width And Height.
Made With Any Combination Of Blocks Or Strips Of Wood, Not More Than 2-1/2 Inches (64 Mm) Wide, Of One Species Of Wood Glued Together (In Butcher Block Fashion), With Joints Staggered In Adjacent Rows.
A Profile Machined On To The Edges Of Stiles, Rails, Mullions, Muntins Or Bars, Adjacent To The Panels, Glazing Materials Or Louvers.
The Outermost Vertical Member Of A Stile And Rail Door.
The Upright Or Vertical Pieces Of The Core Assembly Of A Wood Flush Door. Measurement. The Width Of The Vertical Edge/Stile Is Measured At Its Widest Side (The Wide Side Of A Beveled Door).
Sharply Contrasting Elongated Discoloration Of The Wood Substance.
An Engineered Wood Product That Is Made By Fusing A Network Of Wood Strands Together With A Water-Resistant Adhesive To Produce A Strong, Solid And Stable Product That Has True Structural Properties With Excellent Screw Holding Properties And Very High Split Resistance.
See Worm Tracks.
See Grain.
Strips Of Gummed Paper Used To Hold The Edges Of The Veneer Together At The Joints Prior To Gluing.
See Show Through.
In Knife-Cut Veneer, That Side Of The Sheet That Was Farthest From The Knife As The Sheet Was Being Cut And Containing No Cutting Checks (Lathe Checks).
The Panel Above A Door Or Set Of Doors.
A Deviation In Which One Or Two Corners Of The Door Are Out Of Plane With The Other Corners Of The Door.
A Thin Sheet Of Wood, Rotary Cut, Sliced, Or Sawed From A Log, Bolt, Or Flitch.
See Engineered Construction
Scars In The Wood Generally Caused By The Stems Of Clinging Vines Or By Their Hair-Like Roots, Which Cling To The Tree Trunk. Live Vine Streaks Produce Round Scars. Dead Vine Streaks Contain Either Dead Residue Of The Vine, Or The Remaining Pocket Similar To Bark Pocket. Most Vine Streaks Run Across The Grain, And Therefore, All Vine Streaks Are Considered Defects In Accordance With Restrictions Described In Veneer Grading Rules.
See Gaps.
Any Distortion In The Plane Of A Door Itself And Not Its Relationship To The Frame Or Jamb In Which It Is To Be Hung. The Term Warp Includes Bow, Cup And Twist, Which Are Defined As Follows: Bow-A Flat Wise Deviation From A Straight Line Drawn From Top To Bottom; A Curvature Along The Length Of The Door. Cup-A Deviation From A Straight Line Drawn From Side To Side; A Curvature Along The Width Of The Door. Twist-A Deviation In Which One Or Two Corners Of The Door Are Out Of Plane With The Other Corners Of The Door.
When Referring To Color And Matching, Veneers Containing All Sapwood, Ranging In Color From Pink To Yellow.
An Aggregate Of Resin And Strands, Shreds, Or Flour Of Wood, Which Is Used To Fill Openings In Wood And Provide A Smooth, Durable Surface.
An Assembly Consisting Of A Core And One Or More Edge Bands, With 2 Plies Of Wood Veneer With Laminate, Wood, Or Wood Derivative On Each Side. All Parts Are Composed Of Wood, Wood Derivatives, Fire Resistant Composites Or Decorative Laminates.
Marks Caused By Various Types Of Wood Attacking Larvae. Often Appear As Sound Discolorations Running With Or Across The Grain In Straight To Wavy Streaks. Sometimes Referred To As ‘Pith Flecks’ In Certain Species Of Maple, Birch And Other Hardwoods Because Of A Resemblance To The Color Of Pith.
The Language of Doors
Below Are Some Additional Terms Which Have Been Used To Describe Windows Or Doors Or Their Component Parts. These Definitions Are Not Included In Current Industry Standards.
Areas Of Fiber From Outside A Tree.
White Or Other Color Chalk Marks Used By Mills For Some Form Of Identification Marking Defects For Repair.
Expression For Scars Which Give The Particular Effect Of A Chicken’s Footprint. It Is Caused By Air Roots Or Vines.
Bleeding Resin.